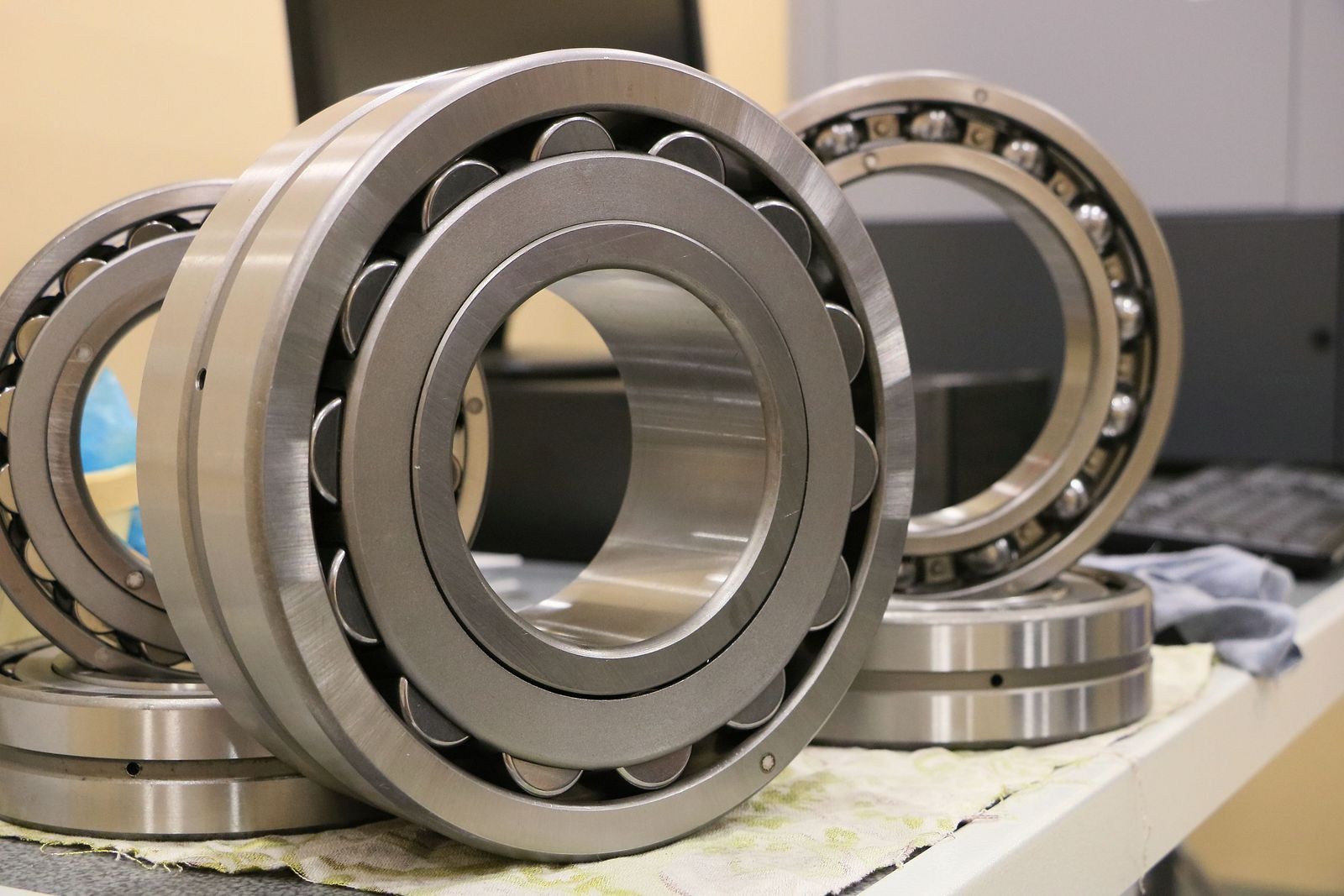
Определение механизма
Сборное устройство является фрагментом опоры, которая поддерживает ось, иную движущуюся конструкцию с необходимой жесткостью. Изделие приводится в действие при помощи колебания, вращения с маленьким сопротивлением, берет на себя нагрузку и передает ее на элементы устройства. Фиксирует в нужной точке.Систематизация
Деталь включает в себя две поверхности в виде колец, тел (шариков, конических, игольчатых, цилиндрических, сферических роликов), сепаратора, отделяющего элементы друг от друга и удерживающего их на определенной дистанции. Внутренние поверхности колец оснащены дорожками (желобами), по которым двигаются металлические тела. Виды подшипником качения различаются и классифицируются по следующим признакам.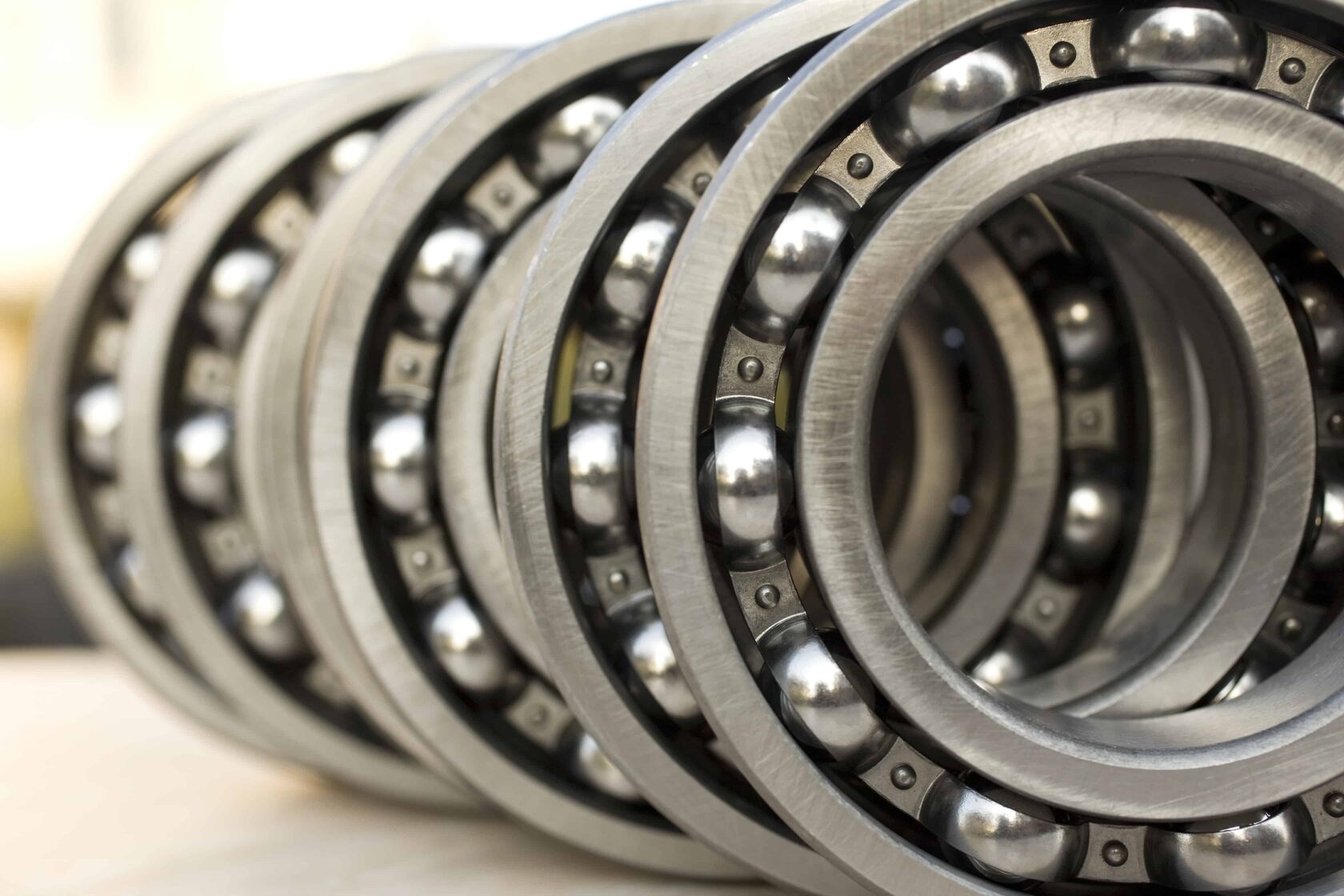
По числу рядов
Конструкции могут быть:• Однорядными. Они состоят из одного ряда тел. Наиболее распространены в тяжелой индустрии. Предназначены для небольшой мощности.
• Двухрядными. В отличие от первого имеют два желоба и выдерживают двойную специфическую тяжесть. Кроме этого, при перекосе более устойчивы в работе.
• Многорядными. Добавление дорожек позволяет увеличить срок эксплуатации механизма. Недостатком является высокая стоимость изделия, поэтому применяется оно в тех отраслях, где это экономически обосновано, и конструкция подвергается максимальной нагрузке.
Вышеописанные виды можно найти в каталоге интернет-магазина торгово-производственной компании «М-Пласт».
По форме элементов
Основные типы и назначение подшипников качения зависят от тел, находящихся внутри механизма:• Шариковые. В роли тела используются металлические элементы обозначение которых прописано по ГОСТу 3722. Буква «Н» обозначает, что в обойме применяются шарики. Размер окружности составляет 18,5 миллиметров, а степень точности – 16. Существуют десять уровней обработки: 200, 100, 60, 40, 28, 20, 16, 5, 3. Иногда на маркировке пишут букву «Б», которая определяет разноразмерность элементов в узле.
• Роликовые.
В виде тел колебания используются:
• Цилиндрические длинные по ГОСТу 22696. D – это номинальный диаметр, L – длина. Буквой «Д» обозначают ролики разной несортированной протяженностью. I, II, IIA, III, IIIA, IV – это классы точности подшипников качения.
• Длинные цилиндрические – ГОСТ 25255. Буква «Б» показывает использование элемента без сортировки по длине и окружности. Степень точности обозначается цифрами по мере снижения уровня обработки: I, II, III. На схеме видно, что английскими буквами указываются параметры изделия (диаметр и длина).
• Игольчатые ГОСТ 6870. Буква « А» говорит о том, что элемент имеет сферический торец, а «В» – плоский конец. Цифра 4 обозначает степень точности.
• Расшифровка конических роликов подшипников качения. D – это показатель номинального диаметра; D 2 – второй величины; L – длина.
• Сферические.
• Асимметричные.
• Комбинированные. Это конструкции, состоящие из разных элементов колебания: шариков и роликов одновременно. Отличительная черта от других – механическая нагрузка распределяется на осевую и радиальную составляющие и равномерно прикладывается между несколькими рядами.
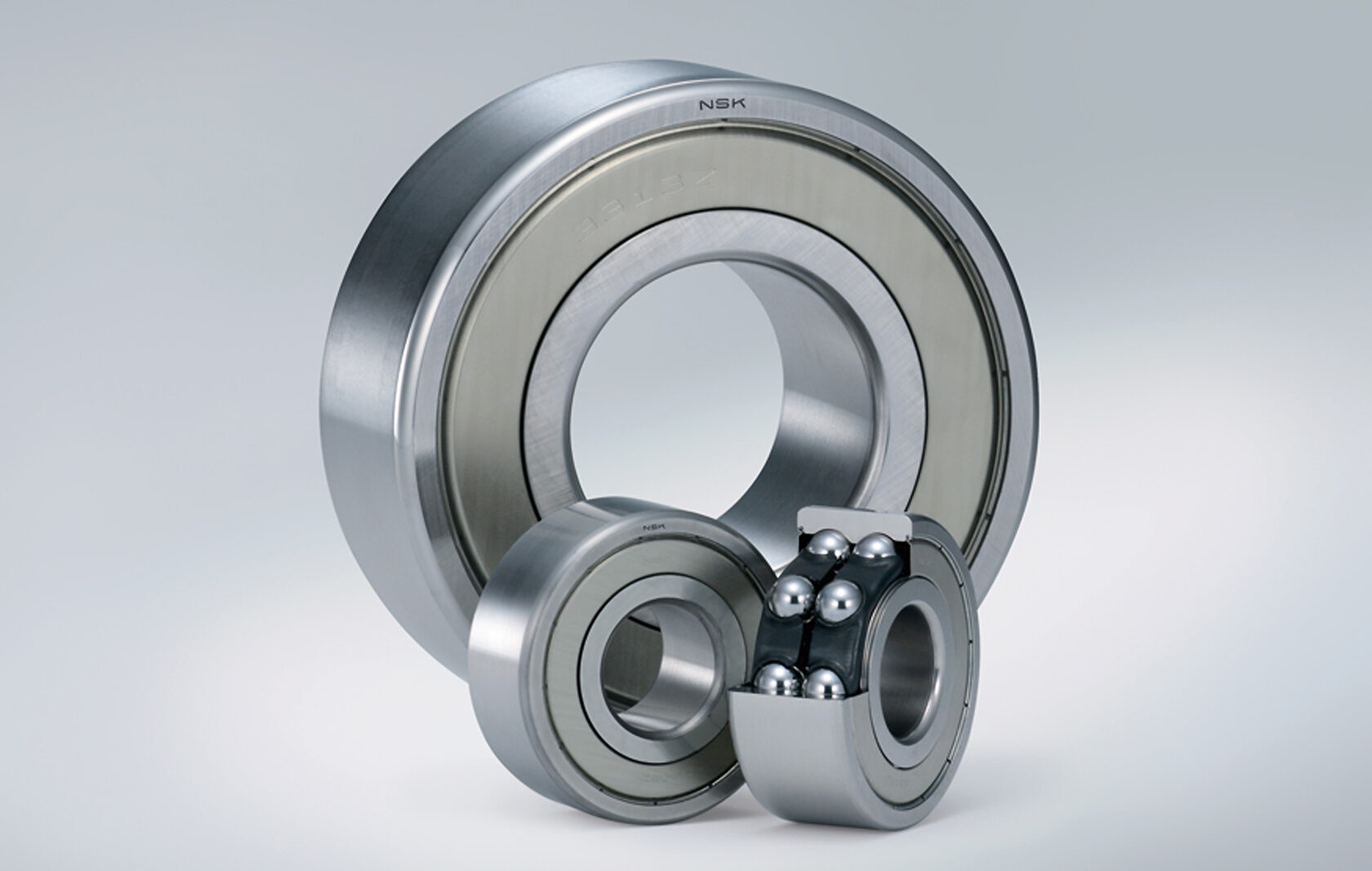
По способу компенсации перекосов вала
Подстроиться под прогибы возможно при помощи самоустанавливающихся опор. Они представляют собой сферические узлы с шариками или роликами, с двумя дорожками для тел на одной поверхности и сферической обработкой другого кольца. Это позволяет при постоянном изменении направления осей сохранять устойчивое соприкосновение элементов без перегруза и ослабления. Свое применение они нашли в сельхозтехнике и агрегатах, где невозможно добиться точного совпадения плоскостей вращения вала и опоры.По способности воспринимать нагрузку
Механизмы делятся на:- Радиальные. Здесь компенсируется напряжение, перпендикулярное оси вращения, то есть идет к наружному диаметру от центра.
- Упорные. Тяжесть подается вдоль оси.
- Радиально-упорные воспринимают усилия в двух направлениях.
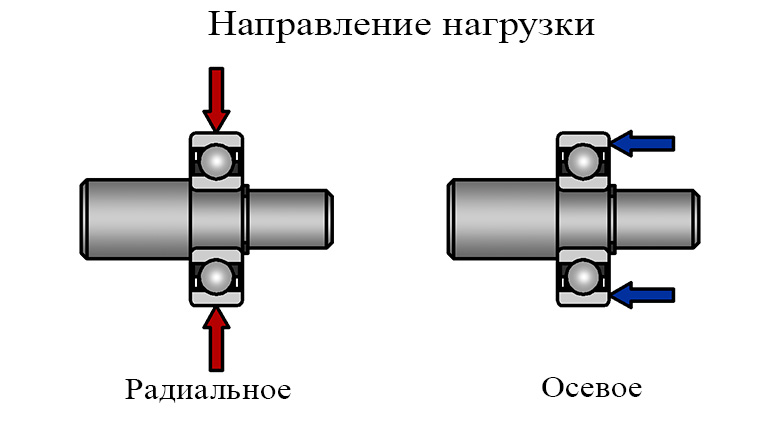
По ширине
В ГОСТе 3395 прописаны устройства по конструктивным особенностям. Ширину обозначает седьмая цифра справа:- узкие – 7;
- нормальные – 1;
- широкие – 2;
- особо широкие – 3, 4, 5, 6.
По габаритам при одинаковом внутреннем диаметре
Выше мы приводили примеры класса точности по международной классификации ISO. В Российской Федерации условные обозначения подшипников качения разделяется ГОСТом на категории:- А – класс точности прецизионный (4), высокий (5), Т и 2.
- В – нормальный (0), высокий (5), повышенный (6), промежуточный (6Х).
- С – повышенный (6), нормальный (0), ниже нормального (7, 8).
Мы привели основные характеристики, по которым квалифицируется узел. Но существуют и другие критерии, такие как: допуски и посадки, зазоры в подшипниках качения, материалы изготовления.
Радиальный просвет играет огромную роль в работе механизма. Это называется расстоянием между элементами колебания (шарики, ролики) и дорожкой на одном из колец. Слишком маленькое значение может привести к заклиниванию, во время эксплуатации происходит нагрев и расширение. Такая посадка именуется у токарей «с натяжкой». Больший размер приводит к постукиванию в самом узле и как следствие, появляется повышенный шум и вибрация. Маркируется зазор по ГОСТу 24810-81 и обозначается цифрами от 0 до 9.
Конструктивные особенности:
- Снимается одно кольцо.
- Имеет защитные шайбы, уплотнители.
- Выпускается с дополнительным отверстием для установки конструкции на валу при помощи закрепительных гаек.
- Изготавливается с участком для увеличения угла перекоса.
- Может иметь борт на наружном кольце.
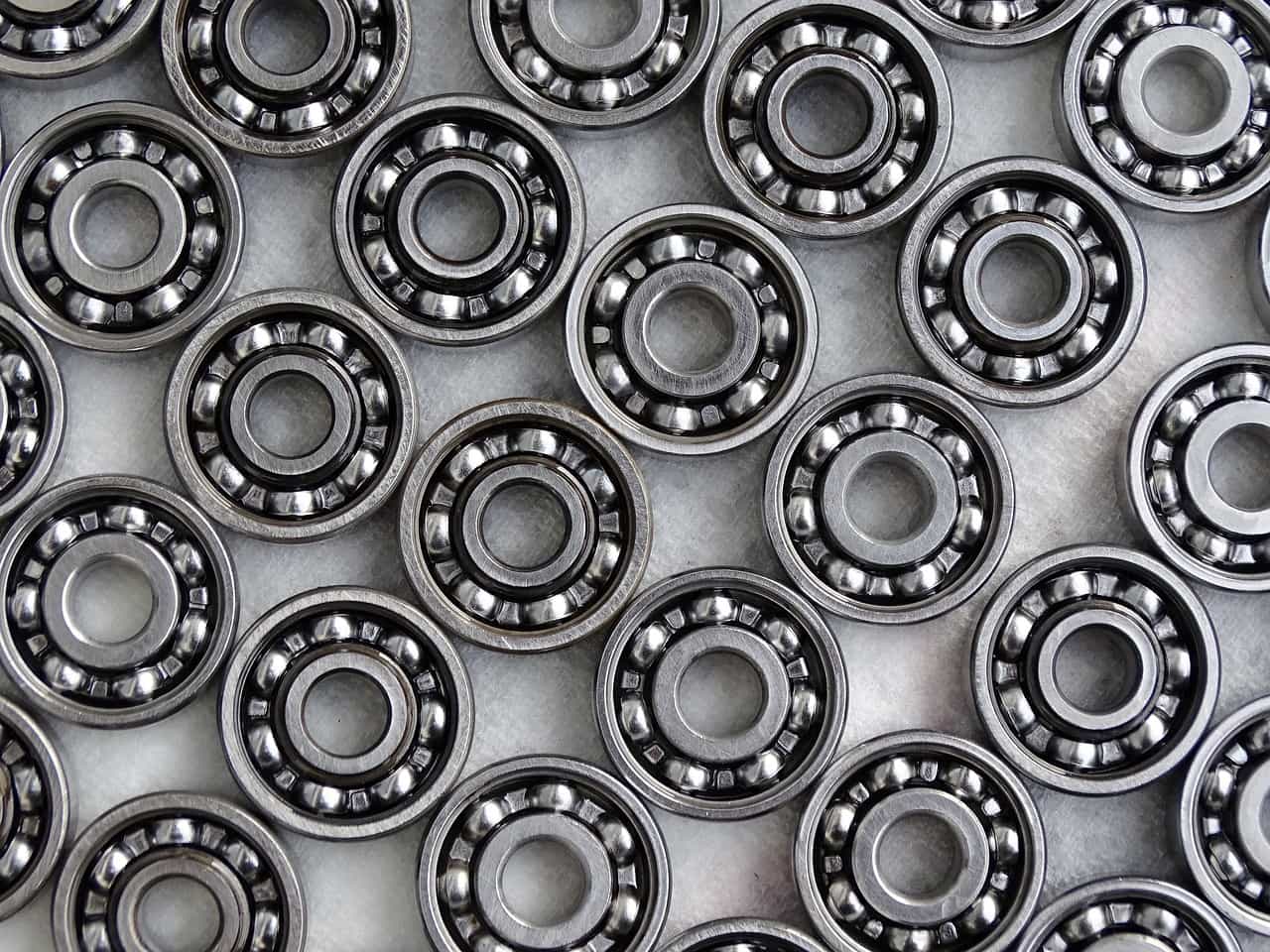
Достоинства и недостатки подшипников качения
К плюсам необходимо отнести:- Намного меньше нагревается, чем узел скольжения из-за низкого трения между деталями.
- Смазка требуется стандартная.
- Эксплуатация этого механизма может производиться в широком диапазоне температурного режима. Выносит экстремальные морозы и жару.
- Имеет небольшие размеры в направлении оси.
- Они разборные, взаимозаменяемые.
- Погрешности при установке вала должны быть минимальными.
- Имеет приличные габариты в радиальном направлении.
- Издает при работе сильный шум.
- При подаче повышенной нагрузки степень износа подшипников качения резко увеличивается.
Подбор и расчет подшипников качения
При выборе узла необходимо учитывать номинальную долговечность. При производстве рассчитывается срок службы, который позволяет 90 процентам изделий из одной группы при одинаковых условиях эксплуатации выдержать нагрузку без возникновения следов усталости. В расчеты входят также динамическая мощность и грузоподъемность. Следует руководствоваться справочниками и документами ГОСТа за № 18854-82 и 18855-82. Там расписаны значения минимальной долговечности, например, для зубчатых редукторов не менее 10000 ч, а для червячных – 5000 ч. Существует технология подбора изделия для эксплуатации в других условиях.Подшипники скольжения и качения имеют принципиальные отличия. Это определяет сферу их применения. За счет того, что в первых происходит постоянное смещение поверхностей относительно друг друга, узел очень критичен к наличию смазочного слоя. Обычно масло подается в зону трения под давлением, так как необходим зазор, обеспечивающий отсутствие прямого контакта. Это сильно усложняет всю конструкцию. Требуется иметь емкость для хранения и слива жидкости, систему подачи, насос и привод. Но при этом, этот механизм выдерживает достаточно большие нагрузки, и при правильной работе имеет неплохой ресурс.
Конструкция и устройство подшипников качения определяет область применения. Эти изделия способны работать как в условиях принудительной смазки, так и в суверенном режиме. Масло, помещенное заводом изготовителем в защищенное пространство, способно обеспечить необходимый ресурс без дополнительного вмешательства.
Узел по конструктивным особенностям несложный. Но деталь является высокоточным механизмом, требующим тщательной настройки всех станков. Между кольцами устанавливаются шарики или ролики. Их удерживает обойма на заданном расстоянии между собой. При этом второе кольцо при эксплуатации остается недвижимым.
Некоторые устройства выпускаются:
- с уплотнительным материалом;
- без разделителя;
- без одного или двух колец;
- поверхности для посадки могут быть с буртиками, выемками в виде цилиндра или сферы, с дырками для подачи смазочного материала, с коническим растачиванием.
Сборка, монтаж и ремонт подшипников качения
Во время конечной операции особое уделяют внимание следующим требованиям:- Все детали должны быть безупречно чистыми, без загрязнений. Если таковы имеются, то происходит промывка бензином или индустриальным маслом в емкости с постоянным подогревом при температуре от 60 до 90 градусов в течение 20 минут. После производится просушка сжатым воздухом.
- Коррозийные пятна очищаются при помощи мягкой ткани с добавлением пасты ГОИ.
- Посадочные поверхности должны соответствовать нормам допустимых пределов (точность).
- Обоймы тщательно обрабатываются керосином, просушиваются и смазываются. Поверхность приводится в порядок, удаляются выбоины и другие повреждения.
- К дефектам подшипников качения относят перекос радиуса закругления галтели на валу. Чтобы это избежать, элемент проверяют радиусомером или шаблоном.
- После завершения сборки узел должен работать плавно и беззвучно, не нагреваясь выше 65 градусов.
- Далее, следует запрессовка детали на вал или в корпус. При установке используется монтажная труба из мягкого металлического сплава, гидравлический или винтовой пресс.
- Крутят вал вручную. Эта операция необходима для устранения перекоса.
- Прилегание узла к заплечным должна составлять не более 0,03 мм. Для этого используется щуп.
Браком является, если на детали имеются:
- Раковины, подверженные основательной коррозией.
- Сепаратор с глубокими трещинами, расслабленными зажимами, выбоинами и вмятинами.
- Зазубрины и крошки от металла на кольцах и телах колебания.
- Неравномерное изнашивание дорожек.
- Материал начинает отслаиваться в виде чешуек.
- Выступление элементов за наружнее кольцо.
Последний операцией становится выбраковка изделия при помощи рук. Зажимают внутреннее кольцо (оно должно быть неподвижным), а наружное вращают. Отремонтированная деталь будет плавно двигаться, издавая глухой звук. Если появились стуки, щелчки и металлический лязг, то узел идет на переплавку.
Выбор лучшей смазки для подшипников качения
Смазочная жидкость необходима для продолжительной эксплуатации механизма. Она минимизирует деформацию и поломку всего узла. Является главным материалом для предотвращения соприкосновения роликов (шариков) с беговыми дорожками, при использовании которой уменьшается трение между этими элементами.Масло или консистентная смазка решает следующие задачи:
- снижает рабочую температуру;
- предотвращает появление ржавчины;
- защищает от попадания грязи, пыли, абразивных частиц;
- уменьшает уровень шума и вибрации.
- Пластичные. Когда невозможно создать герметичность детали, то применяется вязкий материал, который прилипает и удерживается на телах колебания. Чтобы в дальнейшем в процессе работы не происходило выдавливание, аппарат закрывают специальными крышками. Ассортимент разнообразен: «Литол», «Шрус», «Зимол», «Циатим», «Солидол». Вещества, входящие в состав, позволяют работать механизму в условиях радиации, в агрессивных средах, при -50 и +150 градусов.
- Твердые. Смазочным материалом выступает графит.
- Газообразные. Если необходима работа узла без трения, то искусственно нагнетается воздушная подушка, которая не дает прикасаться деталям друг с другом.
- Минеральные, синтетические и полусинтетические масла.